A Cyclingnews special sponsorship feature
Inside S-Works
The welding guru is part of a bigger
team
Photo: © Specialized
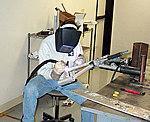 |
The creation of pro-quality bikes used to be the domain of a single
artisan labouring away in a workshop, joining steel tubes with hot brass.
As the guys from Specialized's S-Works division showed us, modern frame
development is a team effort involving design, testing and manufacturing
in a seamless whole.
The team behind the Specialized E5 bikes, as ridden by Mario Cipollini
and the Acqua&Sapone team, answered a few of our questions about the creation
of the frames that Mario and the boys will be rolling out on May 11.
Cyclingnews: There seems to be a three-way development process
at work here between Specialized; teams like Festina and A&S; and Columbus.
How does the development process work exactly - who does what? Who comes
up with ideas? Do the teams say 'we need a stiff bike for this' 'we need
a light bike for that'?
The S-Workers:
Specialized does all of the R&D work at our headquarters in Morgan
Hill, California. We have a dedicated team of people -- including industrial
designers, engineers, framebuilders and product managers -- that work
as a "pod" on the Acuqa & Sapone bikes.
Test pilot
Photo: © Sirotti
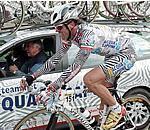 |
Winning team
Photo: © Sirotti
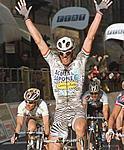 |
The engineers figure out the most effective design using computer modeling
(Pro E to be exact) and finite element analysis. Prototypes are built
and tested, both in the field and in our test lab. Product managers figure
out the best way to complete the bike, components and all.
Ideas come from a variety of sources, and input is encouraged. We're
a tightly knit group constantly challenging one another to improve the
products, and we ride the very bikes that we build. Feedback from the
A&S riders is essentially mandatory (Cipo provides a lot and is quite
exacting) and is taken very seriously.
CN: At the very basis of this sort of development is the raw material.
How do you go about identifying promising aluminium alloys, or is this
the role of Columbus?
SW:
Typically, the frame material for Specialized bikes will evolve
from the design and engineering process. Years ago, we built bikes out
of M2 metal matrix composite. Good stuff, but very limited in its ability
to be shaped and formed, so we had "stick bikes", i.e. bikes with traditional
round tubes. We had some great ideas to make elegant machines that would
be lighter and more aerodynamic, so the R&D guys went shopping for a material
that was more malleable. M4 manipulated alloy was the result. These were
the bikes initially raced by Festina.
M4 worked (and continues to work) very well. But, to make the frames
even lighter, we needed a material with higher tensile strength and one
that would retain more of its integrity after welding. Working with Columbus,
E5 was developed. E5 made its first appearance under Moreau and Casero
last year in the form of the S-Works SL. The frame design conintued to
evolve, ultimately into the E5 AEROTEC frames currently being raced by
Acqua & Sapone.
On test
Photo: © Specialized
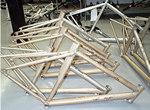 |
In the bike business, a great deal of emphasis is placed on frame material,
particularly from a marketing standpoint. The truth is, though, that material
is only about one-third of the story. Design and manufacturing are equally
important. The "best" material in the world will not yield a great bike
if the design is poor. The "best" material applied to the most intelligent
design will not make for a great bike if the manufacturing quality isn't
up to par. And so on...
Specialized truly sweats every detail in each of these three areas (material,
design & manufacturing) to deliver what we feel to be the best products
to the athletes.
CN: Aluminium alloy frames have been getting lighter and lighter
for the last several years - are the limits being approached? How light
is too light?
SW: Who knows? Asked
this question two years ago, we might have thought that 2.5 pounds was
out of reach for a high performance, durable frame. Today, a stock 56cm
E5 AEROTEC frame weighs less than that (consistently 1.1 kilos), and they're
holding up under extraordinary conditions.
Aerotec
Photo: © Specialized
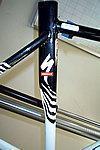 |
By our definition, though, "too light" would mean that either the ride
characteristics of the frames don't meet the riders' needs (e.g. too flexible)
or the frames wouldn't withstand real world riding. We've proven that
producing an excellent frame in the 2.5 pound range can be done. I'd bet
that at some point we'll see them under a kilo (2.2 pounds).
CN: An alloy that contains silicon, copper, manganese, magnesium
and zinc sounds a lot like 7075, but 7075 can't be welded. Is E5 'related'
to 7075 but with the composition tweaked to balance strength and weldability?
SW: The short answer
is "yes". The long answer is confidential (wink, wink!). But seriously,
there are many variables; two of them are of great importance. First is
the ratio of the alloying materials. To get the right balance of strength,
elongation, "weldability", etc., the five alloying elements (hence the
name "E5") must be blended with the base aluminum material in precisely
controlled amounts. Second is the heat treating process that the frames
undergo after welding. The frames must be cured at very tightly controlled
temperatures for precise durations.
Torture
Photo: © Specialized
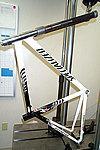 |
The details of both of these critical factors are, in fact, proprietary
to Specialized.
CN: I understand that most A&S riders are on standard frames.
How would you describe the S-Works E5's geometry and handling? What was
the design goal?
SW: Specifying frame
geometry is something of a balancing act. A road racing machine must be
both comfortable and efficient. It needs to be quick & nimble in handling,
yet remain stable at speed.
Specialized approaches this with compact geometry, quite visible in the
frames' sloping top tubes. This design helps place the fit emphasis on
rider postioning rather than standover clearance. The vast majority of
riders can select the frame size that allows for ideal cockpit length
(distance from saddle to handlebars) yet ensure that there's more than
adequate room between him or her and the top tube of the bike.
The smaller triangles seen on compact geometry frames lend themselves
to making a stiffer frame for better handling and improved power transmission.
Also, the design helps lower the center of gravity a bit.
Some rules are made to be broken
Photo: © Specialized
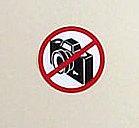 |
In terms of head angles, seat angles, and effectitve top tube lengths,
the frames are pretty "normal" by modern standards. For example, a 56cm
frame has an effective top tube length of 563mm, 73.5 degree head and
seat angles and a 983mm wheelbase.
We produce the S-Works E5 AEROTEC frames in eleven sizes. Such a broad
range of sizes in combination with the versatility of compact geometry
allows for the majority of riders to find their perfect fit in a "stock"
frame.
|